Jord Proxa Africa (Pty) Ltd
Mixed Brine and Effluent Applications
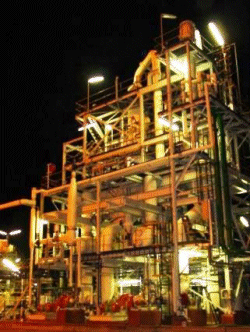
Whilst the treatment of effluents may be regarded as secondary to the main process, effluent plants are now commonly regarded as an essential part of the overall process requiring installation with the initial plant. Reliability, ease of operation and cost effectiveness are just as important, hence the right selection and design of process equipment is essential. Equally important, the need to produce revenue generating by-products from such equipment is accelerating in order to offset the high capital cost of such plants. Although extremely varied, effluent streams tend to have certain characteristics which can pose similar problems in the design of evaporators and crystallisers.
- Effluents are frequently derived from several sources and can contain a wide mixture of components. Physical properties and corrosion characteristics can be poorly defined, necessitating testwork, preferably on a pilot scale.
- Many effluents contain scaling compounds, particularly inversely soluble calcium sulphate. The latter can also form inversely soluble mixed salts with other compounds, e.g. Glauberite, (CaSO4. Na2SO4.H2O). Silica is also a frequent contaminant and may necessitate removal through pre-treatment.
- Some effluents, particularly those organic in nature may cause serious foaming when concentrated. Special designs or anti-foaming agents may be necessary.
- Frequently, some form of pre-treatment may be necessary. Such steps may include neutralisation, softening, clarification and filtration, and may increase the overall capital cost of the plant. However, evaporator performance and/or corrosion characteristics of the liquor may be enhanced, thus reducing costs.
- Many effluents contain chlorides which even if in trace quantities, can concentrate up to high levels in the final brine. Fluorides and other trace elements with a corrosive nature can also be present. Selection of Materials of Construction is therefore crucial and can have a significant impact on the cost of the plant, as high Molybdenum alloys and Titanium tubing are frequently required.
- For higher chloride concentrations, increased Molybdenum content increases resistance to pitting and stress corrosion cracking. Duplex materials such as Alloy 2205 and 2507 can also be employed and these generally have a lower cost. At extremely high Chloride levels in excess of 10 000 ppm (parts per million), "super-alloys" incorporating very high Molybdenum, Chrome and Nickel or alternatively, Monel, are required. Titanium Gr. 2 or 12 is usually employed for heat exchanger tubing.
- Rubber lined steel and plastics (GRP) can be employed in corrosive environments, but increased maintenance requirements and mechanical restraints tend to favour alloy construction.
Click here for more Product Details from
Jord Proxa Africa (Pty) Ltd...